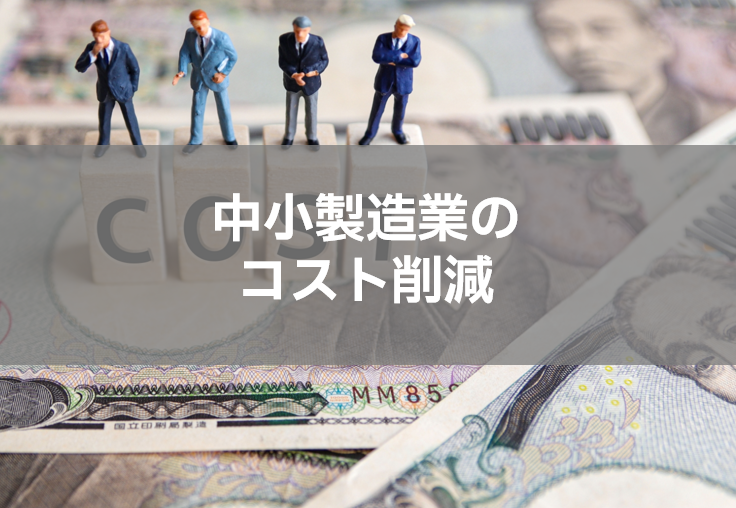
中小製造業が実現するコスト削減の3つの方法
近年、中小製造業はますます競争が激しくなり、コスト削減が極めて重要なテーマとなっています。ここでは、中小製造業が実現可能なコスト削減の手法について、具体的な3つの方法をご紹介します。
まず一つ目は「生産プロセスの見直し」です。多くの中小企業では、生産ラインや作業工程に無駄が生じているケースが少なくありません。生産プロセスを徹底的に分析し、無駄を削減することで、効率的な生産が可能となり、コスト削減につながります。
次に、中小企業が実践できるコスト削減策として「省エネ設備の導入とシステム化」が挙げられます。製造業では多大なエネルギーコストがかかっていますが、省エネ設備の導入によって電力や燃料の効率的な使用が可能となり、コストの削減につながります。
最後に「外部パートナーシップの活用」です。中小企業が自社だけで全ての生産工程を担う必要はありません。外部の専門業者やパートナー企業と協力することで、生産コストを削減し、効率性を向上させることが可能です。
これらの方法を実践することで、中小製造業は今後ますます激化する市場競争に打ち勝ち、持続的な成長を遂げていくことができるでしょう。
目次
コスト削減の基礎知識
コスト削減は中小製造業にとって重要な課題です。
まず、無理なコスト削減は製品品質や生産効率に悪影響を及ぼす可能性があるため、バランスを考えることが重要です。次に、コスト削減は一時的な施策ではなく、長期的な視野で捉える必要があります。生産プロセスや設備の改善など、持続的な取り組みが求められます。
また、コスト削減には「見える化」が不可欠です。経費の内訳や各部門の費用構造を明らかにし、具体的な数値目標を設定することで効果的な取り組みが可能となります。さらに、社内の意識の変革や従業員の参加を促進することも重要です。従業員のアイデアや提案を取り入れることで、持続的なコスト削減が実現できるでしょう。
このように、コスト削減には様々な基礎知識が求められます。適切なバランス感覚や長期的視野、見える化、従業員の参加などを考慮し、効果的なコスト削減施策を積極的に取り入れていくことが重要です。
コスト削減の定義
コスト削減の定義は、企業が製品やサービスを生産・提供する際にかかる費用を削減する取り組みのことを指します。
具体的には、原材料の調達コスト、製造に要する費用、人件費、間接費など、様々な費用項目において削減を目指します。コスト削減は企業の利益向上や競争力強化に直結する重要課題となっています。
コスト削減の取り組みには、無駄の削減や効率化、外部リソースの活用、省エネルギー、原価低減などが含まれます。これらの施策を通じて、企業は収益性の向上や価格競争力の強化を図ることが可能となります。
一方で、コスト削減が過度に行われると品質低下や生産効率の悪化などのリスクが生じることもあります。そのため、バランスを考えたコスト削減戦略が重要であり、長期的かつ持続的な取り組みが求められます。
中小製造業においても、製品の付加価値を損なうことなく、効果的なコスト削減を実現することが重要です。
中小製造業におけるコストの種類
コストには、直接的な生産に係る原材料費や人件費、間接的な経費などがあります。
原材料費や人件費は生産に直結するため、的確な管理が求められます。また、間接費は事務所の光熱費や管理費など、生産ラインとは直接関係しない費用です。積極的なコスト削減には、これらのコストの種類や内訳を的確に把握することが不可欠です。
中小製造業がコスト削減を行う手順
中小製造業におけるコスト削減は、効果的な手順を踏むことが重要です。まず最初に、経営陣や関係者との意思疎通を図り、コスト削減の重要性や目標を共有します。次に、現状のコスト構造や課題を明らかにするためにデータを収集し、問題点を特定します。
その後、優先順位をつけて解決すべき課題を特定し、改善のための具体的な施策を検討します。
また、コスト削減を実行する際には、社内外のステークホルダーとの協力が不可欠です。従業員や現場の声を取り入れながら、適切な施策を打ち出し、実行することが重要です。さらに、専門家やコンサルタントの知見を活用し、的確なアドバイスを得ることも効果的です。
ただし、コスト削減は一過性の取り組みではなく、継続的な取り組みが求められます。定期的に改善の成果を評価し、必要に応じて修正を加えながら、着実にコスト削減を進めていくことが重要です。以上の手順を踏むことで、中小製造業はコスト削減を実現し、競争力を強化できます。
1. 既存コストの把握
コスト削減を行う前に、まずは既存のコストをしっかり把握することが重要です。
具体的には、月次や年次の財務諸表を分析し、どの項目にどれだけのコストがかかっているのかを明らかにします。また、各部門やプロセスごとにコストを細かく分解し、どの部分が特にコストを押し上げているのかを特定します。
この過程で、無駄な経費や過剰なコストが明らかになることがあります。
また、一見小さなコストの積み重ねが全体のコストに与える影響を理解することも重要です。こうした分析を通じて、どの部分に改善の余地があるのかを把握し、具体的な施策を練る土台となります。つまり、既存コストを把握することで、無駄な出費を見つけ出し、効果的な改善策を講じることが可能となります。
2. 改善対象の洗い出しと削減策の検討
改善対象の洗い出しと削減策の検討は、コスト削減の取り組みにおいて重要なステップです。
まず、生産プロセスや業務の中で無駄や浪費となっている要因を徹底的に洗い出し、優先順位をつけて改善対象を特定します。また、コスト削減に繋がる可能性のある項目や範囲を広く捉えることが大切です。この段階では、現場レベルからのアイデアや提案を取り入れることで、具体的な課題や改善のポイントを明確化します。
次に、洗い出した改善対象に対して具体的な削減策を検討します。削減策はコスト削減だけでなく、効率化や品質向上にも繋がるものであることが理想です。経営陣や現場の関係者との討論やアイデア出しを通じて、最適な削減策を導き出します。また、短期だけでなく長期的な視点も踏まえ、持続可能な改善策を検討することが重要です。
3. 削減策の実施とマニュアル整備
削減策を実施する際は、まず計画を策定し、関係者に周知徹底することが重要です。
具体的な行動計画を立て、担当者を明確にし、スケジュールや目標を定めます。その上で、関係部署と連携を図りながら、段階的に改善策を実施していきます。変更点や進捗状況を定期的に報告し、透明性を確保します。
さらに、改善活動の成果や手順をまとめたマニュアルを整備することが有効です。このマニュアルは、今後同様の課題に直面した際にも指針となり、組織全体でのコスト削減を促進します。各ステップや責任者、進捗管理の方法などを明文化し、情報の共有を図ります。削減策の実施においては、計画的かつ体系的なアプローチが成果をもたらします。
コスト削減の3つの手法
中小企業が実践できるコスト削減の手法にはさまざまな方法があります。
まず一つ目は「生産プロセスの見直し」です。多くの場合、生産ラインや作業工程に無駄が生じていることがあります。生産プロセスを徹底的に分析し、無駄を削減することで、生産効率を向上させ、コストを削減することができます。
次に挙げられるのが「省エネ設備の導入とシステム化」です。製造業では多大なエネルギーコストがかかっていますが、省エネ設備を導入することで、電力や燃料の効率的な使用が可能となり、コストを削減することができます。
そして最後に「外部パートナーシップの活用」があります。全ての生産工程を自社で行う必要はなく、外部の専門業者やパートナー企業との協力によって、生産コストを削減し、効率性を向上させることができます。これらの手法を活用することで、中小企業は競争力を向上させ、持続可能な成長を実現することができるでしょう。
手法1: 生産プロセスの見直し
生産プロセスの見直しは、中小企業にとって非常に効果的なコスト削減手法です。まず、生産ラインや作業工程を詳細に分析し、そこで発生している無駄やムダを洗い出します。その後、無駄を削減し効率的な工程に改善するための改善計画を立てます。例えば、生産段取りの見直しや不要な在庫の削減などが効果的な手法です。
さらに、従業員と協力して現場での意見交換を行い、生産の現場からのアイディアを取り入れることも重要です。これにより、具体的な改善の着想を得ることができます。また、生産設備の適切な保守管理や最新の技術導入なども効果的な手法と言えます。生産プロセスの見直しは、効率性を向上させるだけでなく、従業員のモチベーション向上や安全面でもプラスの効果が期待できます。改善のポイントを把握し、段階的に進めることで、中小企業における生産プロセスの効率化とコスト削減につながるでしょう。
手法2: 省エネ設備の導入とシステム化
中小企業のコスト削減策の一環として、省エネ設備の導入とシステム化が重要な役割を果たします。
まず、製造業におけるエネルギー消費は大きなコストの要因となっています。そのため、省エネ設備の導入によって電力や燃料の効率的な使用を実現することが重要です。さらに、システム化によって機械の自動制御や監視が可能となり、生産プロセスの効率化につながります。これによって、エネルギーコストを削減し、競争力を強化することが期待できます。
また標準化された業務、定型的な業務にあたっては、システム化や、PRAの導入を検討しましょう。
さらにExcelで作成する文書、見積作成のような複雑な手順を踏まないと作成できないものについては専用のクラウドサービスの導入がおすすめです。
手法3: 外部パートナーシップの活用
外部パートナーシップの活用は、中小企業がコスト削減を図る上で重要な手法の一つです。例えば、IT化、DXの取り組みの一部を外部の情報システム専門業者に委託することで、自社内の人員を最大限に活用し、コストと時間の節約が可能になります。また、パートナーシップを活用することで、専門的なノウハウや技術を持つ企業と提携することができ、自社の競争力強化につながります。
さらに、外部パートナーシップを通じて、製品開発や市場開拓など新たな取り組みにも挑戦することが可能となります。外部の専門家やパートナー企業との連携によって、自社の弱点を補い、より効果的な業務遂行が可能となるでしょう。
ただし、外部パートナーシップを活用する際には、信頼できるパートナーや契約条件について慎重に検討することが不可欠です。しっかりとしたパートナーシップ戦略を策定し、適切なパートナーとの連携を築くことが成功につながります。外部パートナーシップの活用によって、中小企業は効果的なコスト削減と成長戦略を実行し、競争力強化を図ることができます。
コスト削減の成功事例
事例1: 余剰品の発生防止
ある製造業では、無駄の発生を防ぐために生産ラインを見直しました。それまでの生産プロセスにおいて、材料の無駄や過剰な在庫が発生していたため、生産ラインを細かく分析し、無駄を減らす工夫を行いました。
具体的には、不良品の発生要因を特定し、原因別の生産ラインを設けることで、不良品の削減に成功しました。さらに在庫管理の見直しにより、余剰在庫を減らし、ストックコストの削減にも成功しました。
この取り組みにより、余剰品の発生を防止すると同時に、納期の短縮、在庫の削減、生産効率の向上といった効果も上げることができました。新たな生産プロセスの導入によって、コスト削減を実現する成功事例として注目されています。
事例2: 稼働率の見える化
ある製造業では、機械の稼働率を可視化することでコスト削減に成功しました。従来は機械の稼働時間や停止時間が把握しづらかったため、無駄な待ち時間が多く生じていました。
稼働率を見える化するため、各機械の稼働状況をリアルタイムでモニタリングし、停止時間や稼働率の推移をデータ化しました。これにより、生産ラインの稼働状況を把握し、停止時間の削減に成功しました。
具体的な改善施策としては、稼働率の低い時間帯にメンテナンス作業を集約するなど、稼働率向上に向けた計画的な取り組みを行いました。その結果、無駄な停止時間が大幅に削減され、生産効率が向上したことでコストの削減につながりました。
事例3: 拠点間の情報共有
製造業において、複数の拠点や工場を有する企業では、拠点間の情報共有が重要な課題となります。そこで、ある製造企業では、拠点間の情報共有を強化することでコスト削減に成功しました。
まず、異なる拠点間での情報共有を円滑に進めるため、コミュニケーションツールの導入が行われました。ビデオ会議システムやチャットツールの活用により、遠隔地の拠点間でリアルタイムな情報共有が可能となり、無駄な出張コストを抑えることに成功しました。
また、情報共有における電子化も進められました。各拠点の情報をデジタル化し、クラウド上で共有することで、情報の確認や共有が容易となり、情報伝達のヒューマンエラーを減らし、生産プロセスのミスを減らすことに成功しました。
さらに、社内での情報共有を促進するため、情報発信のプロセスやルールを整備し、情報の鮮度と正確性を確保しました。結果として、拠点間の情報共有がスムーズに進み、コストを削減するだけでなく、業務の効率性向上にも貢献しました。
コスト削減の注意点
コスト削減は中小製造業にとって重要ですが、注意が必要なポイントもあります。
まず、過度なコスト削減は品質や生産性に悪影響を及ぼす可能性があります。例えば、材料や部品の安価な代替品の選定には品質低下や故障率の上昇などのリスクが潜んでいます。また、人件費の削減によって労働者のモチベーション低下や技能不足などが生じる可能性も考慮しなければなりません。
さらに、長期的な視点でのコスト削減計画が必要です。一時的な財務上の利益のみを追求するのではなく、将来のビジネスの持続可能性や競争力も考慮した計画が必要です。また、コスト削減に適した施策を見極めるためには、徹底的な現場調査やデータに基づいた分析が欠かせません。
最後に、社内の関係者や従業員とのコミュニケーションと協力が欠かせません。コスト削減策の実行には従業員の理解と協力が不可欠であり、そのためには綿密なコミュニケーションが重要です。従業員の意見やフィードバックを取り入れながら、計画を進めていくことが成功の鍵となります。
これらの注意点を踏まえつつ、効果的なコスト削減施策を実践することで、中小製造業は持続可能な成長と競争力を築いていくことができるでしょう。
必要な経費は削減しない
製造業におけるコスト削減の際、必要経費は削減すべきではありません。例えば、品質管理や安全対策にかかる経費は妥協できません。これらは事業の信頼性と継続性に直結する重要な部分であり、適切な投資が必要です。同様に、研究開発や新技術導入にかかる費用も将来の競争力を保つ上で欠かせません。こうした観点から、必要な経費は惜しむことなく投資することが重要です。
長期的視点でのコスト削減
コスト削減に取り組む際には、一時的な利益だけでなく、将来の競争力や持続可能な成長を見据えた長期的な視点が欠かせません。具体的な施策として、次のような取り組みが重要となります。
まず、製品やサービスの品質向上を目指すことが重要です。品質が向上すれば顧客満足度が向上し、リピート率やブランド価値の向上につながります。また、品質の向上によって故障率や不良品の発生が減少し、それに伴うリコールやクレーム処理のコストも削減できます。
次に、環境負荷の低減を目指す取り組みも重要です。省エネ設備の導入やリサイクル利用、廃棄物削減などの施策は、環境への配慮と経済的なメリットを同時に得られる一石二鳥の取り組みとなります。
さらに、従業員のスキルアップや生産性向上に注力することも重要です。継続的な教育研修や効率的な業務プロセスの改善によって、生産性を向上させることができ、結果的にコスト削減と競争力強化につながります。
これらの長期的な視点でのコスト削減施策を実践することで、中小製造業は持続可能な成長と競争力強化を実現していくことができます。
過度なコストカットは逆効果
コスト削減は企業にとって重要ですが、過度なコストカットは逆効果になる可能性があります。
過度なコストカットによって、品質が低下したり、顧客満足度が低下したりすることもあります。品質やサービスの低下によって、顧客離れが進み、結果的に売上減やブランド価値の低下につながることが考えられます。
また、過度なコストカットによって従業員のモチベーションが低下し、離職率の上昇や労働生産性の低下などにつながる可能性があります。従業員は会社の財産であり、そのモチベーションを維持することは重要です。適切なバランスを保ちながら、コスト削減を進めることが求められます。
適切なバランス感覚を持って、過度なコストカットを避け、品質や効率性を損なわずにコスト削減を行うことが、中小製造業における持続可能な成長のために重要です。
まとめ
中小製造業が実現可能なコスト削減の手法について、3つの方法をご紹介しました。
生産プロセスの見直し、省エネ設備の導入、外部パートナーシップの活用といった具体的なアプローチが能動的なコスト削減を促進します。生産工程における無駄の解消や効率的なエネルギー使用、専門業者との協力などが重要です。
中小企業はこれらの手法を実践することで、持続可能な成長と競争力の強化が期待できます。コスト削減に向けて積極的な取り組みを行うことで、業界内での地位を確固たるものにし、市場での競争力を強化していくことが不可欠です。
中小企業のDXや見積書作成でお困りの方はぜひ一度弊社までお問い合わせください。
HOME > コラム記事一覧